Understanding Porosity in Welding: Exploring Reasons, Effects, and Prevention Techniques
As experts in the welding sector are well mindful, understanding the reasons, impacts, and prevention methods connected to porosity is critical for achieving robust and reputable welds. By delving right into the origin creates of porosity, analyzing its harmful results on weld quality, and exploring effective prevention strategies, welders can improve their knowledge and skills to produce premium welds consistently.
Typical Root Causes Of Porosity
Contamination, in the type of dirt, grease, or rust on the welding surface, produces gas pockets when heated, leading to porosity in the weld. Improper protecting takes place when the shielding gas, frequently used in procedures like MIG and TIG welding, is unable to completely shield the molten weld pool from responding with the bordering air, resulting in gas entrapment and succeeding porosity. Additionally, insufficient gas insurance coverage, typically due to inaccurate flow prices or nozzle positioning, can leave components of the weld vulnerable, enabling porosity to create.
Effects on Weld Top Quality
The presence of porosity in a weld can considerably jeopardize the total quality and honesty of the bonded joint. Porosity within a weld produces spaces or cavities that deteriorate the framework, making it a lot more prone to splitting, rust, and mechanical failure.
Additionally, porosity can impede the efficiency of non-destructive testing (NDT) strategies, making it testing to discover various other issues or stoppages within the weld. This can cause considerable safety problems, especially in crucial applications where the structural honesty of the welded parts is vital.

Prevention Techniques Overview
Offered the damaging impact of porosity on weld top quality, effective avoidance methods are essential to keeping the structural honesty of bonded joints. One of the primary avoidance techniques is detailed cleansing of the base materials prior to welding. Pollutants such as oil, oil, rust, and moisture can add to porosity, so making certain a clean job surface is crucial. Appropriate storage of welding consumables in completely dry conditions is additionally important to stop dampness absorption, which can cause gas entrapment during welding. In addition, selecting the suitable welding specifications, such as voltage, present, and take a trip speed, can assist minimize the danger of porosity development. Making sure appropriate protecting gas circulation and coverage is one more critical avoidance technique, as inadequate gas insurance coverage can result in climatic contamination and porosity. Appropriate welder training and accreditation are essential for carrying out preventative measures efficiently and consistently. By integrating these avoidance methods right into welding techniques, the event of porosity can be substantially decreased, leading to more powerful and extra reputable welded joints.
Relevance of Appropriate Protecting
Appropriate protecting in welding plays a critical duty in protecting against climatic contamination and guaranteeing the integrity of bonded joints. Shielding gases, such as argon, helium, or a mix of both, are commonly made use of to secure the weld pool from responding with elements airborne like oxygen and nitrogen. When these reactive elements enter contact with the warm weld swimming pool, they can trigger porosity, resulting in weak welds with reduced mechanical homes.
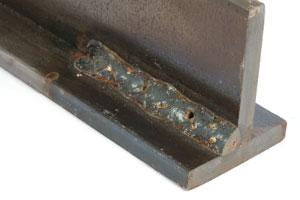
Insufficient shielding can lead to different defects like porosity, spatter, and oxidation, endangering the structural stability of the bonded joint. For that reason, sticking to correct protecting techniques is important to generate top quality welds with marginal defects and ensure the durability and integrity of the welded components (What is Porosity).
Monitoring and Control Techniques
Exactly how can welders successfully keep an eye on and regulate the welding procedure to ensure ideal results and stop problems like porosity? One trick approach is via using advanced monitoring innovations. These can include real-time tracking systems that offer comments on specifications such as voltage, present, take a trip speed, and gas flow prices. By continually monitoring these variables, welders can identify discrepancies from the optimal conditions and make immediate adjustments to stop porosity formation.

Additionally, implementing correct training programs click reference for welders is necessary for keeping an eye on and regulating the welding procedure successfully. What is Porosity. Enlightening welders on the value of preserving regular criteria, such as appropriate gas shielding and take a trip speed, can help protect against porosity issues. Normal evaluations and certifications can additionally make sure that welders are skillful in tracking and managing welding processes
Moreover, the use of automated welding systems can boost tracking and control capacities. These systems can exactly regulate welding criteria, minimizing the likelihood of human mistake and ensuring constant weld high quality. By integrating advanced tracking technologies, training programs, and automated systems, welders can efficiently check and manage the welding process to minimize porosity flaws and attain premium welds.
Verdict
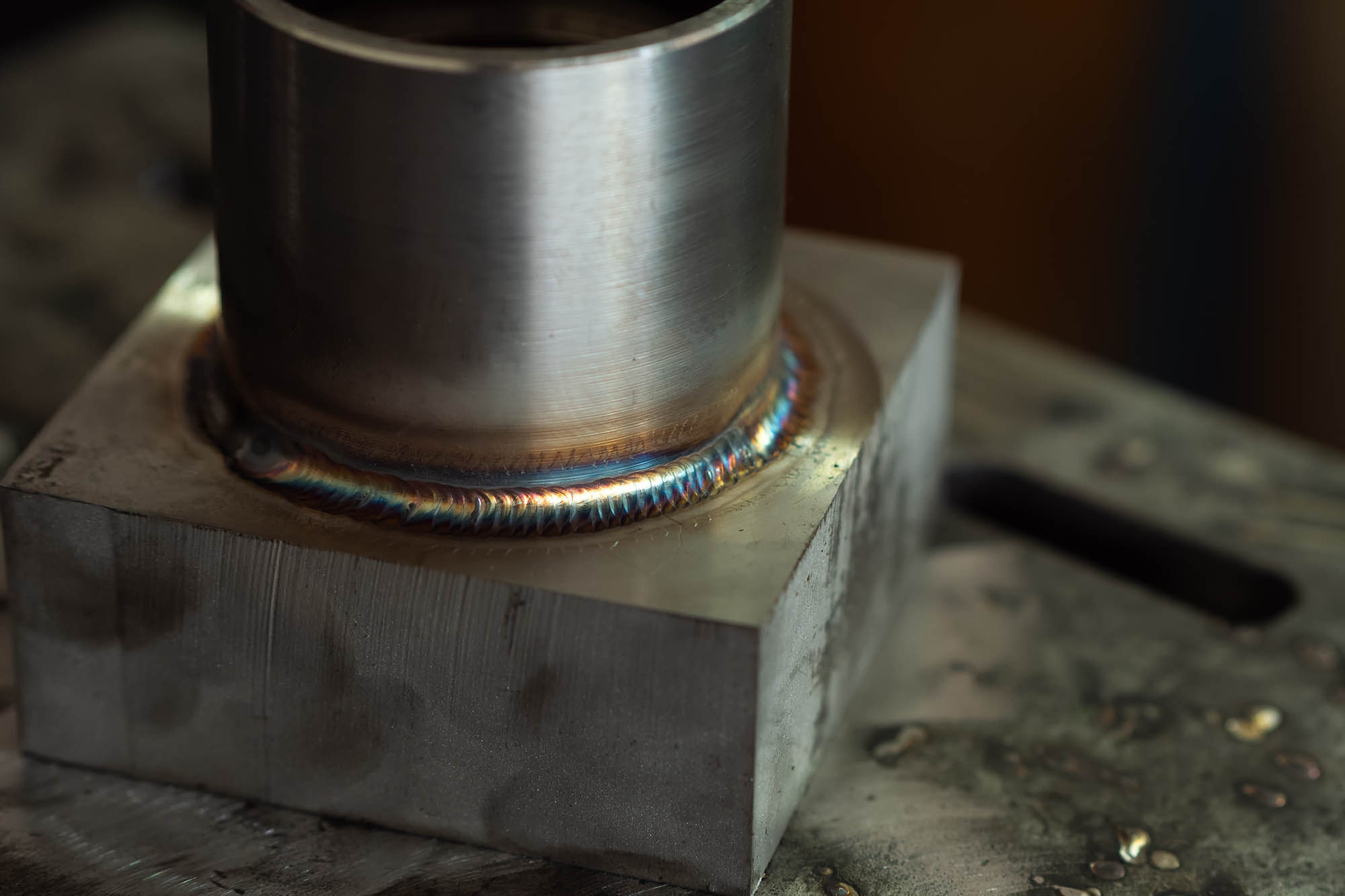
Comments on “What is Porosity in Welding: Recognizing Its Reasons and Enhancing Your Skills”